Let’s say you’re opening a warehouse or already have one. You have the space and some products, but the hard part comes: putting your facility together. To do this successfully, you need to know how to organize your warehouse to become more efficient and effective at processing orders promptly while keeping costs low.
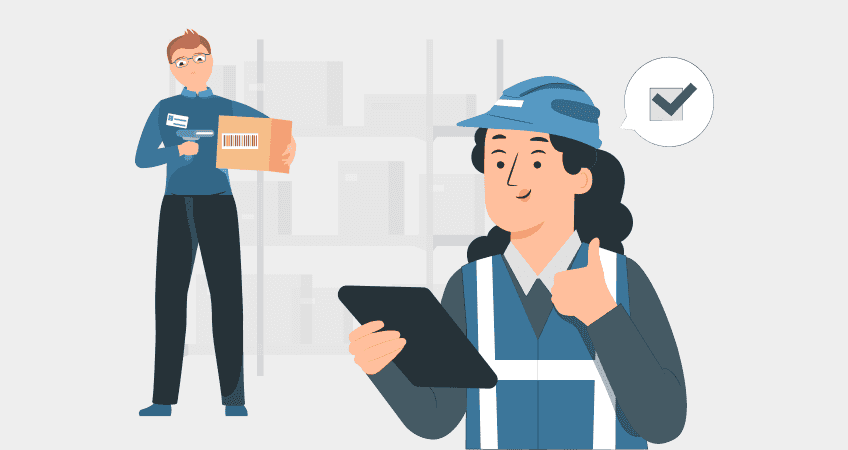
What is warehouse optimization?
Warehouse optimization process is optimizing warehouse space and operations to meet the warehouse needs. It involves identifying and placing the most profitable products in the most efficient locations and reducing additional unnecessary efforts for warehouse operations.
Warehouse optimization techniques can also increase efficiency by removing unnecessary items from the warehouse or adding more storage space as well as enhancing day-to-day operations.
Warehouse optimization can be done manually, but it is most effective when automated with a Warehouse Management System (WMS). The warehouse management solution will track inventory levels and analyze sales trends to determine optimal product placement, which will help you store more efficiently and save money on storage costs.
Why is optimization important?
Warehouses are a big part of the supply chain and can play a significant role in your business. However, it's essential to understand why warehouse optimization is crucial for your warehouse. Here are some of the reasons why it's so important.
Speed of delivery
The faster you can get products from your warehouse to customers, the better. Your customers will appreciate that you have fast shipping options available. This will help you build your brand as an efficient company that delivers what customers want when they want it.
Product quality
If your warehouses aren't optimized, there's a good chance that some of your products may not be up to standard. Customers may not receive what they were expecting or paid for. In addition, using outdated technology in your warehouses can cause delays in receiving and shipping products and incorrect inventory levels, leading to lost sales and revenue losses for your business.
Cost savings
Warehouse optimization has been shown to save businesses money by reducing inventory management, transportation, and operational costs. By having more efficient processes in place, warehouses can reduce their overall costs while also increasing productivity levels within their facilities through better resource management practices such as automation which helps cut down on labour.
Benefits of warehouse optimization
Reduced operating costs
A warehouse isn't just where products are stored and where employees spend their time. If you reduce your warehouse's operating costs by optimizing your processes and operations, you'll be able to lower the amount you spend on utilities and other expenses associated with running the warehouse.
Improved performance
In the same way that optimizing your warehouse allows you to save money, it can also help improve your performance. By reducing wasted time and increasing productivity in your warehouse, you'll be able to increase sales and boost profits for your company.
Cost savings through better planning and inventory control
If you're not optimizing your warehouse, you're leaving money on the table. The average cost of inventory management is over $3 per hour—and if you don't have the right management tools in place before or after an order comes in, that number could rise even higher! Warehouse optimization is critical to cutting costs while maintaining high customer service and availability levels.
Better customer service and product availability
It helps you maintain better control of your inventory and orders, reducing the risk of losing money on products that aren't selling or have been sold but are still waiting for delivery. You'll also ensure that your customers get exactly what they want when they order.
Better cash flow management
Warehouse optimization helps to improve cash flow management by reducing storage costs, which can be considerable. It also improves inventory accuracy and provides better access to parts.
Challenges of warehouse management (Without WMS)
The biggest challenge for warehouses that don't use a warehouse management system (WMS) is the lack of real-time visibility. This makes it difficult for all the stakeholders to track the movement of their products, which can lead to delays in receiving or delivering goods or even loss of products in transit.
Another challenge that these warehouses would encounter is the inability to make informed decisions about whether to extend a contract or not. They cannot account for performance indicators such as customer satisfaction, return rates, and theft rates.
The lack of flexibility poses another problem for these warehouses. Some industries may be seasonal and require large amounts of inventory during peak seasons but may not be able to afford to hold on to it during leaner times when demand is lower.
To better understand warehouse management problems, let's divide the categories.
Inbound
- Inbound order management - A mistake in any one of these processes can collapse the entire workflow, which means redoing all the steps from the start
- Put-away - finding difficulty in searching a location for putting away the product to the right location
Operations
- Inventory Management system – Difficult to manage inventory
- Track movement / Product visibility - Unable to track inventory movement and limited visibility of products
- Manual warehouse management – Manual work occurs due to human error and consumes more time to perform warehouse operations
- Find the missing product - Having difficulty finding the missing product in case of theft
- Stock Count – Counting stock manually consumes more time, and human error can affect accuracy.
Outbound
- Outbound order management – struggling in finding accurate stages of sales order.
- Order picking – Inaccuracy in picking could lead to more time to pick the right product.
- Verify to be shipped product - Sometimes, the wrong product is shipped, increasing the return ratio; verification is not done during the shipping.
Ways how WMS helps to optimize warehouse
Inbound
- System suggested put away
One of the best ways to opitmize warehouse is by putting away products as they arrive at the location. WMS can help make this process more efficient by auto-suggesting the location for the product so that you can put it away as soon as it arrives at the warehouse.
- Smoothen Inbound Order management
WMS gives you a comprehensive view of each activity during the inbound order process. You can see how many orders are being processed when they were received and needed to be picked up, what types of items are being ordered, and so on.
This will help you identify bottlenecks or slowdowns in your operation and ensure that your employees are working as efficiently as possible.
- Reduce human errors
RFID-enabled Warehouse management solutions improve your inventory process and can help reduce human errors. When you have a decent warehouse management system, you can increase your accuracy and performance. This will reduce the number of human errors in your warehouse.
Operation
- Inventory Visibility
Inventory visibility is a crucial component in the process of managing inventory. It helps you track all the products, keep them in your warehouse, and check their status at any time. It also provides users with information about their current inventory levels and lets them know what they need to do next.
- Stock Count
An efficient WMS helps automate warehouse functions such as stock count, rework, and other operational aspects of business processes. It uses real-time data to identify and prioritise inventory movements so that the employees don't have to spend all day counting boxes or walking the aisles of your warehouse.
- Manage Return Product
The return management module in a WMS efficiently manages and identifies the return products with different features. It creates a database of products that have been returned, how many were returned, and what kind of product was returned.
This helps you identify which products are being returned and why. You can then use the information to change your process or improve overall inventory management.
Outbound
- Measure and reduce travel time
Warehouse management systems (WMS) help to optimize warehouse operations by reducing travel time and increasing productivity. You can store the most frequently picked items in accessible locations using WMS.
This allows you to reduce the amount of time employees spend travelling around the warehouse and increases their efficiency at work.
- Consider a multi-order picking process
A multi-order picking process is one of the most efficient ways to increase picking speed. When a warehouse receives multiple orders for the same product, it is necessary to have a process to handle these inbound orders. A WMS can help by allowing multiple orders for one product to be processed together.
This helps to reduce labour costs for the warehouse because it reduces the number of employees needed to complete these tasks.
With WMS, warehouses can use different picking methods like Batch Picking and Zone picking with multi-order picking.
- Analyze performance
With WMS, you can create KPIs and dashboards to analyze your warehouse's performance. KPIs are metrics that help you understand how well your warehouse is doing, so you can make adjustments as necessary.
KPIs give you a way to see if the performance of your warehouse is meeting or exceeding your expectations.
They allow you to adjust quickly and easily based on what's happening at the moment.
- Picking accuracy
Picking accuracy is the degree to which a given product is picked from the warehouse. It's a vital warehouse efficiency metric because it can track how much inventory is wasted due to picking errors.
As picking covers roughly 55% of the cost of warehouse operating expenses, warehouses should adopt different approaches like Analyzing product velocity and error data. Automate as much as possible by adopting Warehouse management solutions.
Final thoughts
So, how do you take your warehouse from good to great? The key is ensuring you have the right tools and processes in place. In the end, the warehouse management system (WMS) is a tool that helps optimize your warehouse operations.
The WMS is not just a technology, it's a way of thinking—it provides you with an overall goal and strategy for managing your warehouse as a whole.